3 min read
Technology Development: When the Galileo mission’s probe entered the Jovian atmosphere in December 1995, it experienced temperatures twice as hot as the surface of the sun, and required carbon phenolic shields to protect its onboard payload from the intense heat. Since that mission, NASA has not flown a spacecraft that required protection from such extreme heat. Recently, however, the NRC Planetary Science Decadal Survey has recommended that NASA consider in situ science missions to Venus and Saturn as a high priority in the New Frontiers competed mission set. To reach the surface of these planets, missions will require heatshields that are capable of withstanding very extreme entry environments, but are not as heavy as the previously used carbon phenolic heat shields.
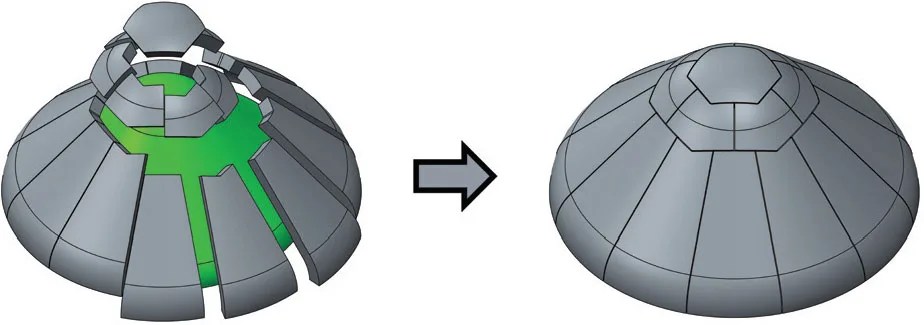
To respond to this need, NASA and its industry partners are developing an innovative way to design and manufacture a family of ablative thermal protection system (TPS) materials using commercially available weaving technology. This new approach—called Heat-shield for Extreme Entry Environment Technology (HEEET)— leverages the way three-dimensional (3-D) weaving is used to manufacture aircraft parts made of carbon composite materials. To manufacture TPS materials with the desired properties, fibers of different compositions and variable yarn densities are accurately placed in a 3-D structure. Three-dimensional weaving extends the traditional twodimensional (2-D) weaving by interconnecting woven material in the third direction, enabling the manufacturing of materials that are more robust to the entry environment than traditional 2-D woven materials. The panels are then infused with resins and cured to lock the fibers in place. Using advanced modeling, design, and manufacturing tools to optimize the weave for overall improved performance, the HEEET project has manufactured a new family of TPS materials and tested them for a wide variety of entry conditions.
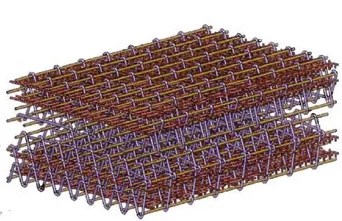
Impact: Depending on the mission design, peak heat-flux during entry can reach about 10,000 W/cm2 for both Venus and Saturn, and the peak pressure can range up to about 1,000 kPa. HEEET is currently being designed to withstand these conditions and at the same time provide mass efficiency far superior to that of the heritage carbon phenolic material used for TPS in legacy missions. In addition to providing thermal protection, the 3-D weave also increases the mechanical robustness of the TPS material.

Status and Future Plans: The HEEET team is currently supporting multiple New Frontier proposals in anticipation of a New Frontiers Announcement of Opportunity at the end of 2016. Plans call for the HEEET project to mature and deliver technology for infusion into selected missions long before Key Decision Point B—the decision gate leading to the period in the mission lifecycle where a project begins preliminary design and completes required technology development. In 2015, HEEET milestones included demonstration of the ability to form and resininfuse a representative acreage HEEET tile, the spherical nose cap. In addition, the project successfully completed an arc jet test series to support material response model development and in support of the seam design. This testing allowed the project to refine its material response model in support of TPS sizing and to narrow the seam design trade space.
Sponsoring Organization: SMD funding of HEEET began in 2013, when the Planetary Science Division (PSD) jointly funded a year-long formulation study with the Space Technology Mission Directorate’s Game Changing Development (GCD) Program. In fiscal year (FY) 14, the HEEET project was formally funded jointly by SMD and STMD, as a four-year effort to further mature technology for advanced TPS. NASA’s industry partners include Bally Ribbon Mills in Bally, Pennsylvania and Fiber Materials Inc. in Biddeford, Maine.