Hubble's Impact on Human Spaceflight
Quick Facts
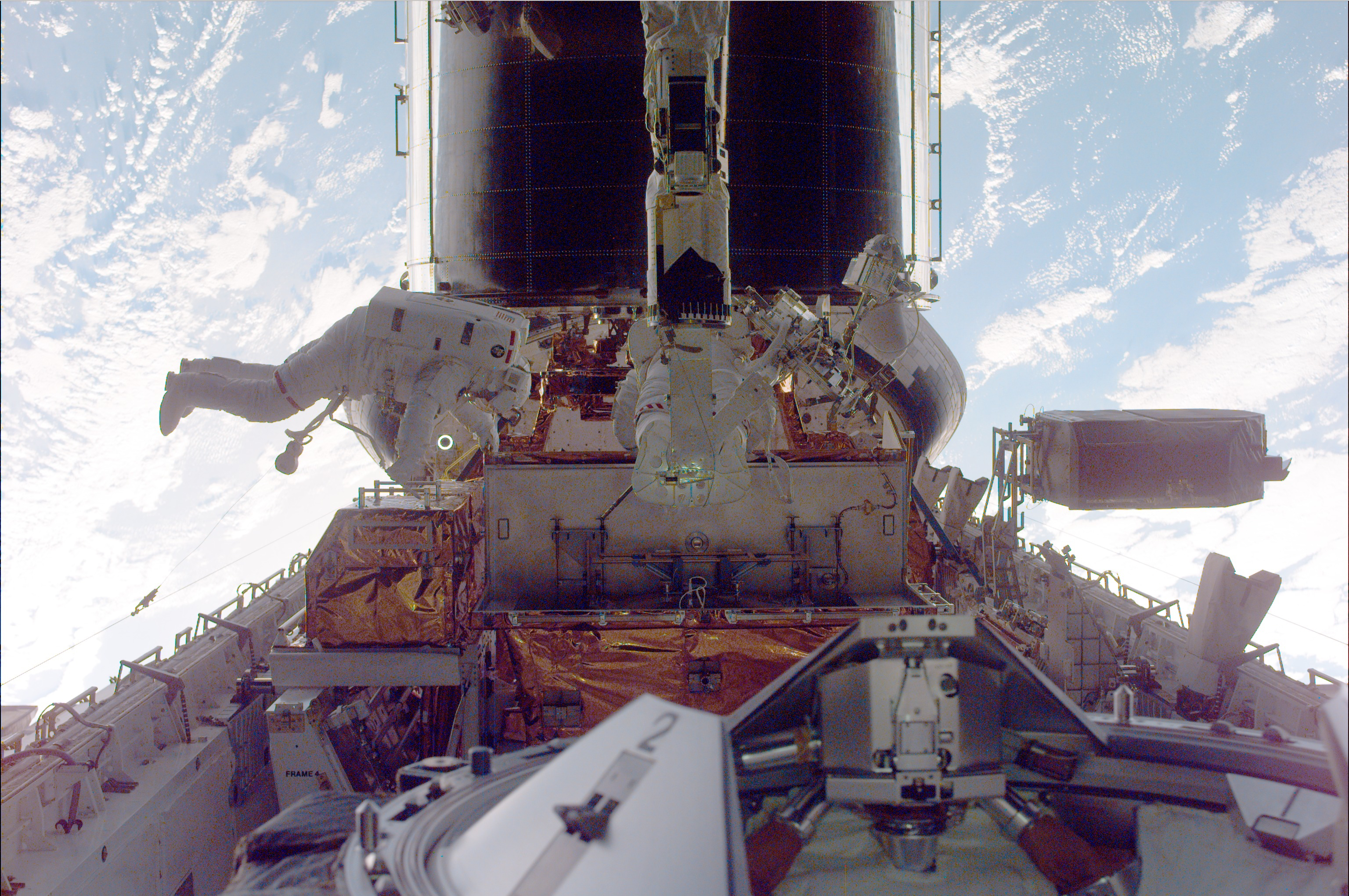
The Hubble Space Telescope’s more than 30 years in orbit were punctuated by periodic visits from astronauts that kept the telescope functioning smoothly and equipped it with increasingly powerful instruments. These visits provided NASA with a unique opportunity: to observe men and women working together in space while developing ways to improve that experience —make it smoother, easier, and less dangerous.
The lessons learned from Hubble’s missions have gone on to influence human spaceflight and alter the way people work in the airless, gravity-free environment beyond our planet’s boundaries.
The Right Tool for the Job
There’s no popping out to the hardware store for a different tool when you’re on the job in space. Engineers, working closely with astronauts as they trained for and worked on Hubble, developed hundreds of custom tools. As astronauts put those tools to the test, the tools were revised and refined to work as best as possible under unique constraints, like bulky spacesuits, stiff gloves, an intensely hazardous environment, and the tendency for materials to float away when unattended. Tools had to be designed to prevent fatigue and to avoid wasting precious time to accomplish all the tasks of the mission.
For example, during the first servicing mission, astronauts found that a tool designed to work with electrical and cable connectors on the telescope was clumsy to use, so the tool was redesigned with that feedback for following missions. During Servicing Mission 3B, when astronauts had to swap out a power control unit with over 36 densely packed electrical connectors, all those revisions — including a final one specific to this job — paid off in the design of the High Torque Connector Tool, which proved to be up to the task.
One of the most famous tool developments for Hubble was the Pistol Grip Tool, first used on the second servicing mission. Today it is a standard tool for working on interfaces in space and is one of the workhorse tools on the International Space Station. The Pistol Grip Tool is very similar to a powered screwdriver with a few important alterations.
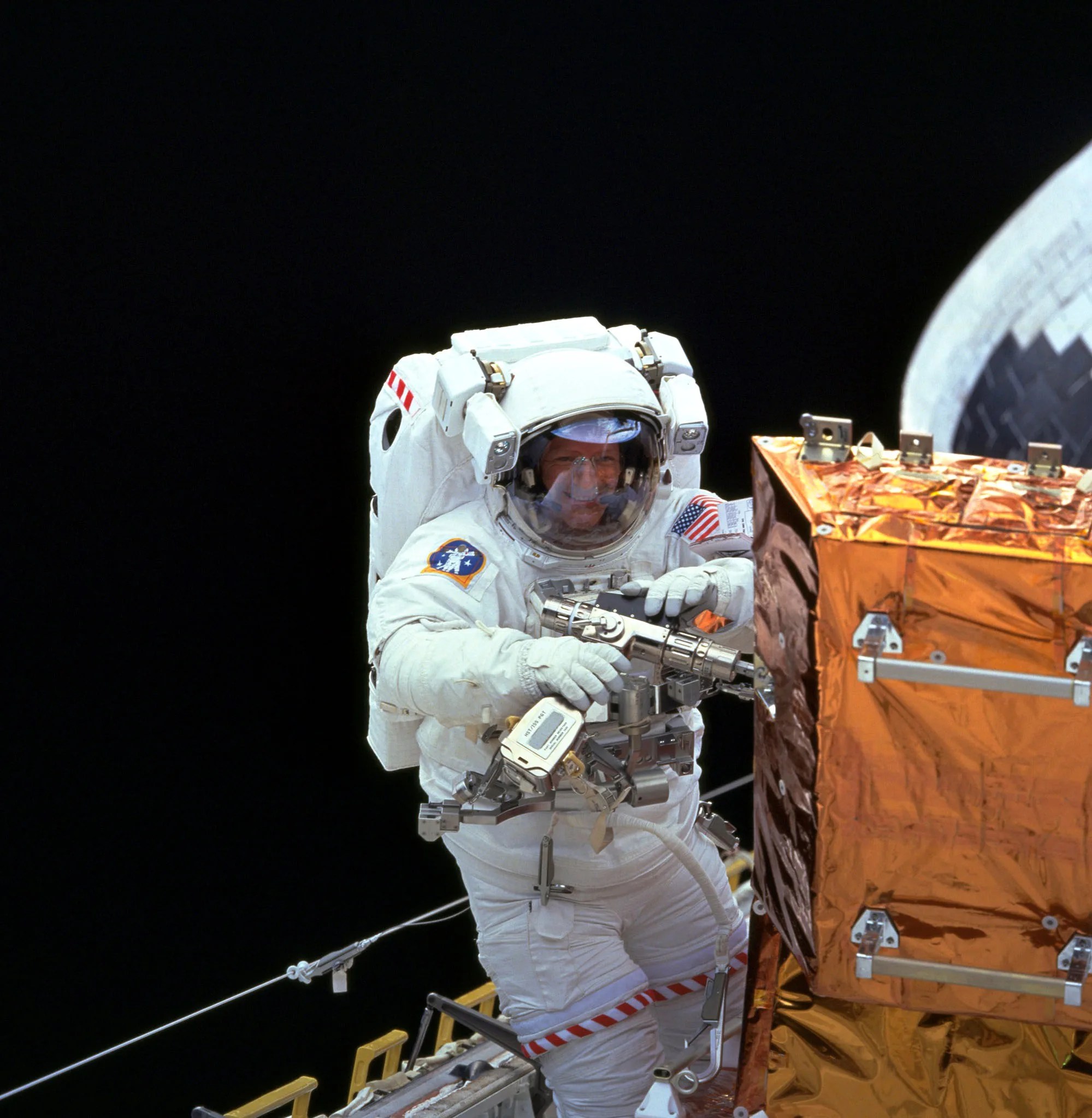
First, it’s incredibly programmable: Astronauts can pre-set the speed, number of turns, direction, and other features for each task. Secondly, it records information about the tasks it performs, like speed and torque, creating a record that becomes extremely useful later. For instance, if an astronaut working on the same part of Hubble later encountered a tough bolt, the torque could be checked against the record and adjusted accordingly.
The Mini Power Tool, a similar but faster, smaller device created to remove 111 tiny screws during the repair of the Space Telescope Imaging Spectrograph (STIS) during Servicing Mission 4, is also a candidate for use on future missions. The Fastener Capture Plate, built to keep those 111 very small screws from floating away and getting into places where they shouldn’t, was the model for a similar tool used in 2019 to repair a particle physics experiment module on the International Space Station.
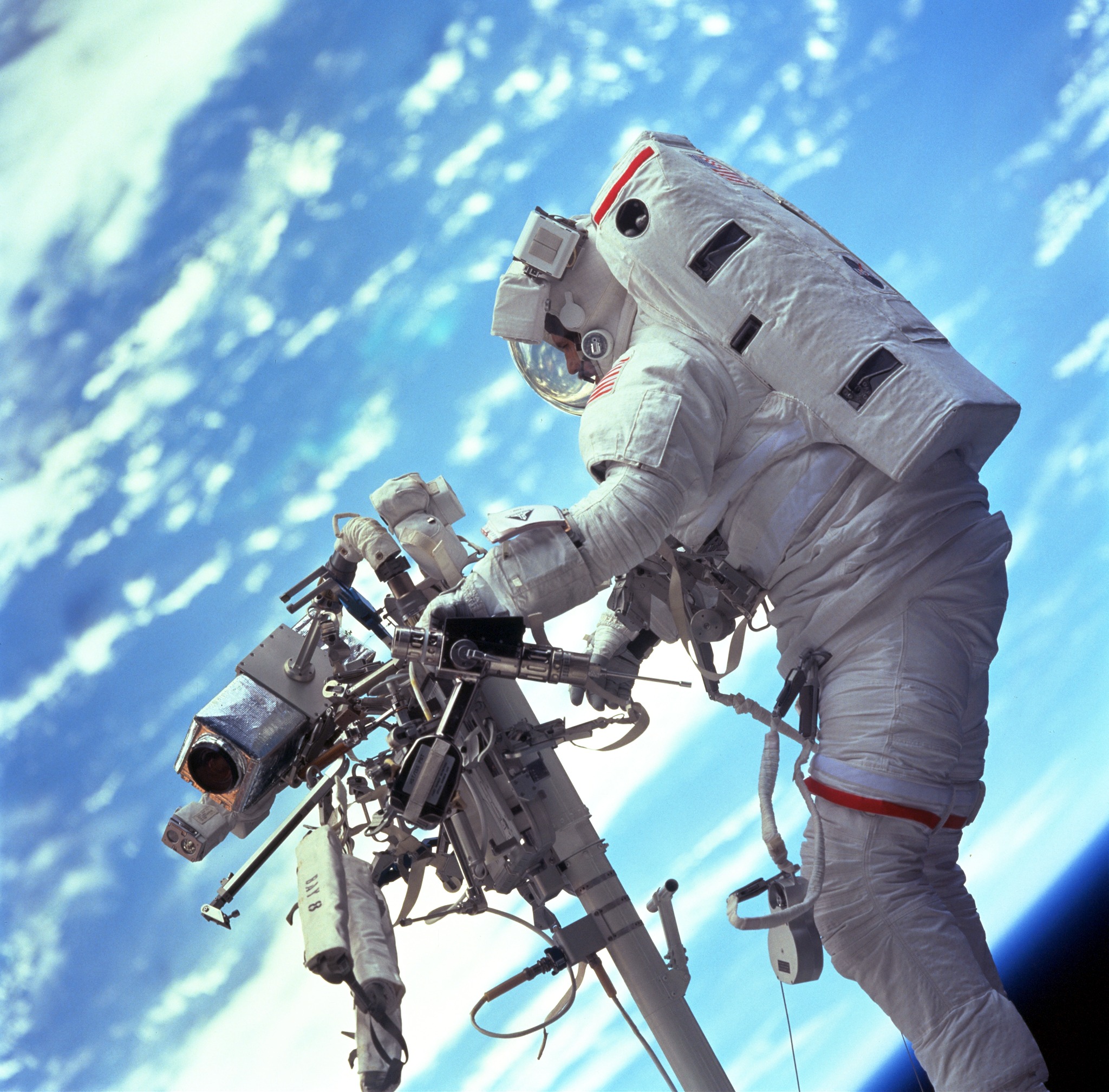
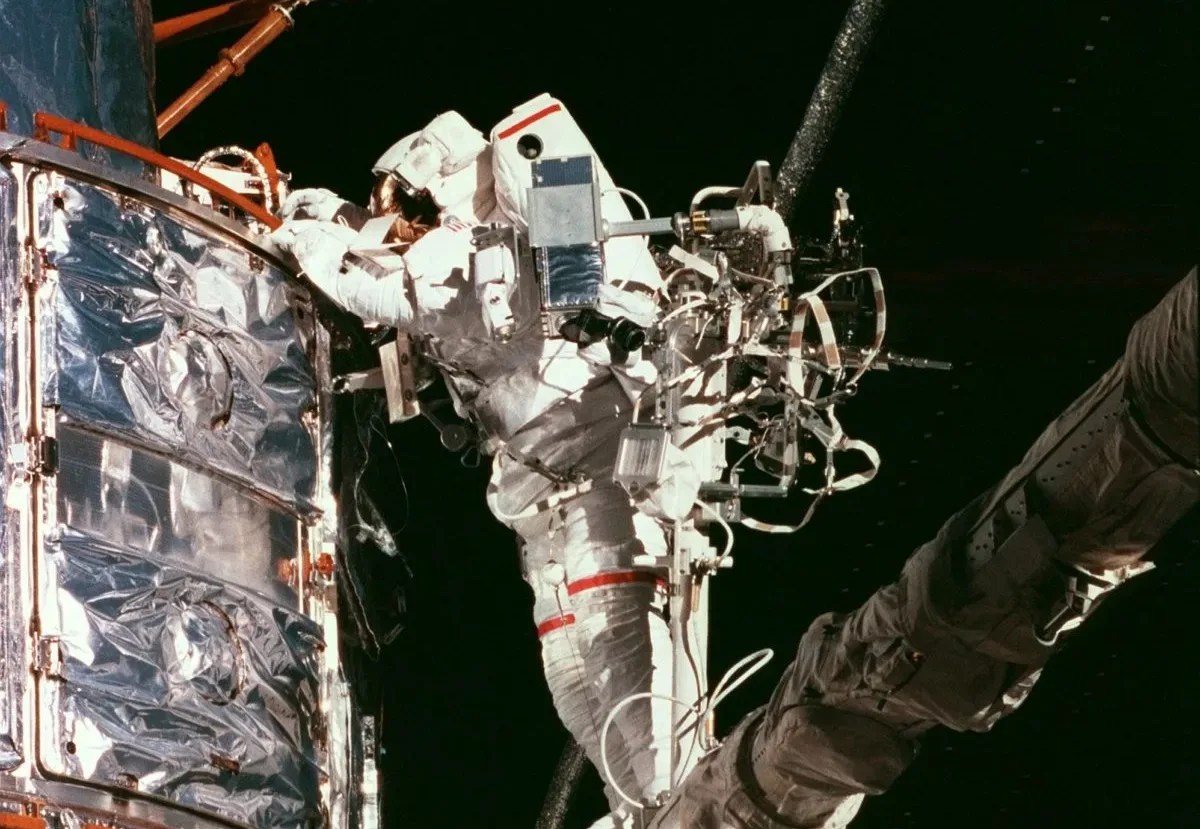
Train, Train, and Train Again
The Hubble servicing missions weren’t based on the premise of expecting the unexpected, but in taking as much of the unexpected out of the equation as possible. Intricate and precise replicas of Hubble and its components were built for use on the ground and in the water tanks at Johnson Space Center and Marshall Space Flight Center. Astronauts practiced with them constantly before missions, using what they learned to continuously redesign and refine both techniques and tools.
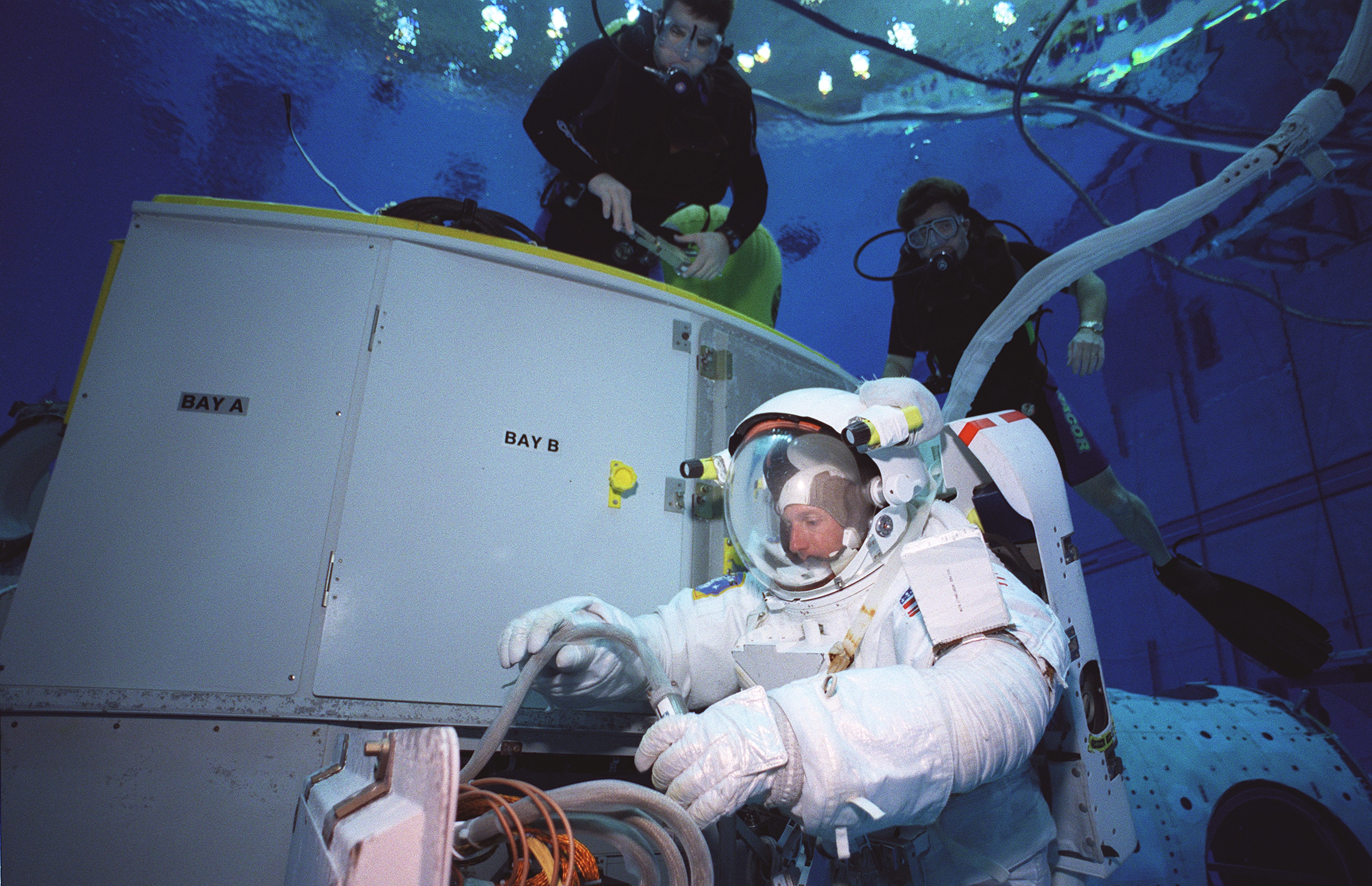
John Grunsfeld, an astronaut on three separate Hubble missions, recalled practicing every night for a year on a detailed replica of the Power Control Unit before replacing it on Servicing Mission 3B. “I wanted to know every connector personally, all the features of the keying of the circular connectors, the cable routing, even the pins and sockets of each connector (which I would have to inspect in orbit),” he wrote.
Astronauts struggled with some of Hubble’s doors on Servicing Mission 1, leading to the construction of simulated doors that future teams would practice on, learning not just the mechanics of how they opened and closed but how two astronauts should work together to operate them. Whenever astronauts encountered unexpected problems during the servicing missions — a given with Hubble enduring the wear and tear of its harsh space environment — they would be absolutely familiar with the components they were seeing and how they worked.
The replicas were also critical when the Hubble team decided to attempt repairs that were not previously envisioned, as on Servicing Mission 4, when astronauts made several key fixes that went far beyond swappable modules to opening up instruments and replacing internal components. Astronauts and engineers were able to work together on the replicas to revise tools and techniques that would make those repairs possible.
With so much training, servicing missions became almost choreography, with astronauts knowing exactly where to place their hands, turn their bodies, manipulate items, apply pressure, and so on, in precise conjunction with their spacewalking partner. Because nothing compared with the reality and complexities of a mission in space, if a spacewalk was scheduled for six hours, astronauts were sure to demonstrate that they could accomplish it in four and a half hours in the water tank.
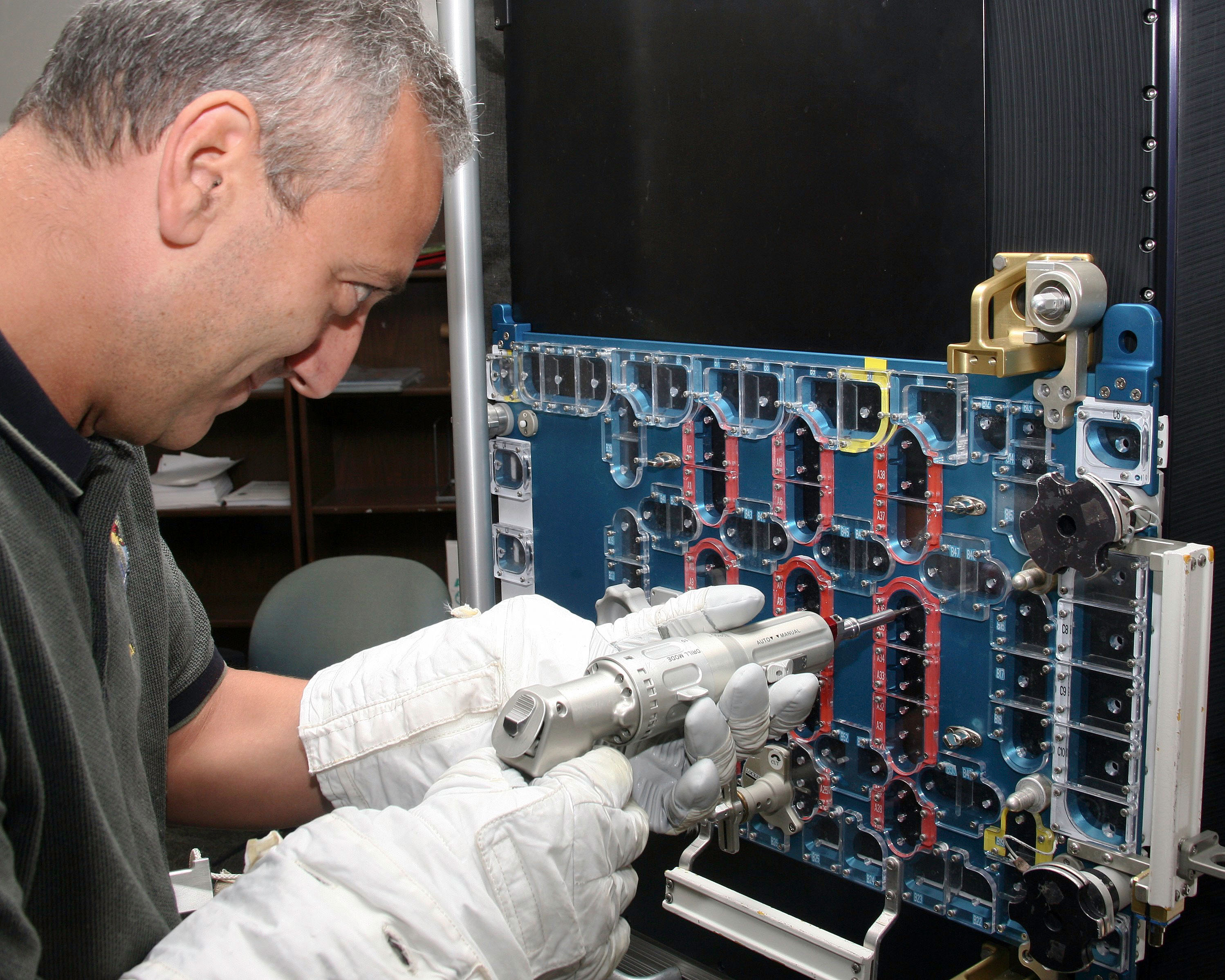
Being able to test on the ground, test in the water tank, change your designs, go back in and do it again and again. Test, test, retest and train, train and retrain. That was the most fundamental process … what I think is the reason for all our success.

Frank Ceppolina
former associate director of NASA’s Satellite Servicing Capabilities Office
That degree of training, preparation, and development is expensive, and the associated price tag must also be carefully considered. Today’s missions may choose to invest in that long-term expense, while others decide to make their mission a one-and-done deal that ends when the technology wears out. But the success of Hubble’s servicing missions provided an important blueprint for the activities that led to effective and streamlined spacewalks.
Expanding NASA’s Knowledgebase
Hubble’s servicing missions provided many opportunities to increase or refine the knowledge NASA had about how things work in space. Knowledge and skills related to rendezvousing and docking with another object in orbit translated to other missions with the ISS and Russia’s MIR, and Soyuz spacecraft. One of the areas where Hubble was particularly helpful was in providing analysis of the vibrations from jets firing. The vibrations and the frequencies at which they resonate can damage or even tear interacting spacecraft apart if they aren’t just right. Those investigations are critical for every spacecraft, current and future, and the analysis performed for Hubble servicing missions helped improve those studies.
Another area where Hubble stood out was the degree of human interaction with the telescope and its components. Astronauts actively grasped and at times even struggled with the telescope, gripping onto parts like handrails. These actions called attention to the importance of items like glove checks, during which astronauts will take time to make sure that their gloves are undamaged. By checking their gloves during one servicing mission, astronauts found yellow paint was flaking off Hubble’s handrails, which could possibly contaminate the telescope’s components during the mission. Astronauts would eventually install covers over the guardrails to solve the issue.
Frequent visits to the telescope also provided a treasure trove of knowledge about how components stand up to a lot of unattended time in space. The cracking of Hubble’s insulating blankets, for example, led NASA to seriously study the conditions affecting the blankets in space at a molecular level. This drove NASA engineers to develop better versions that were later installed on Hubble.
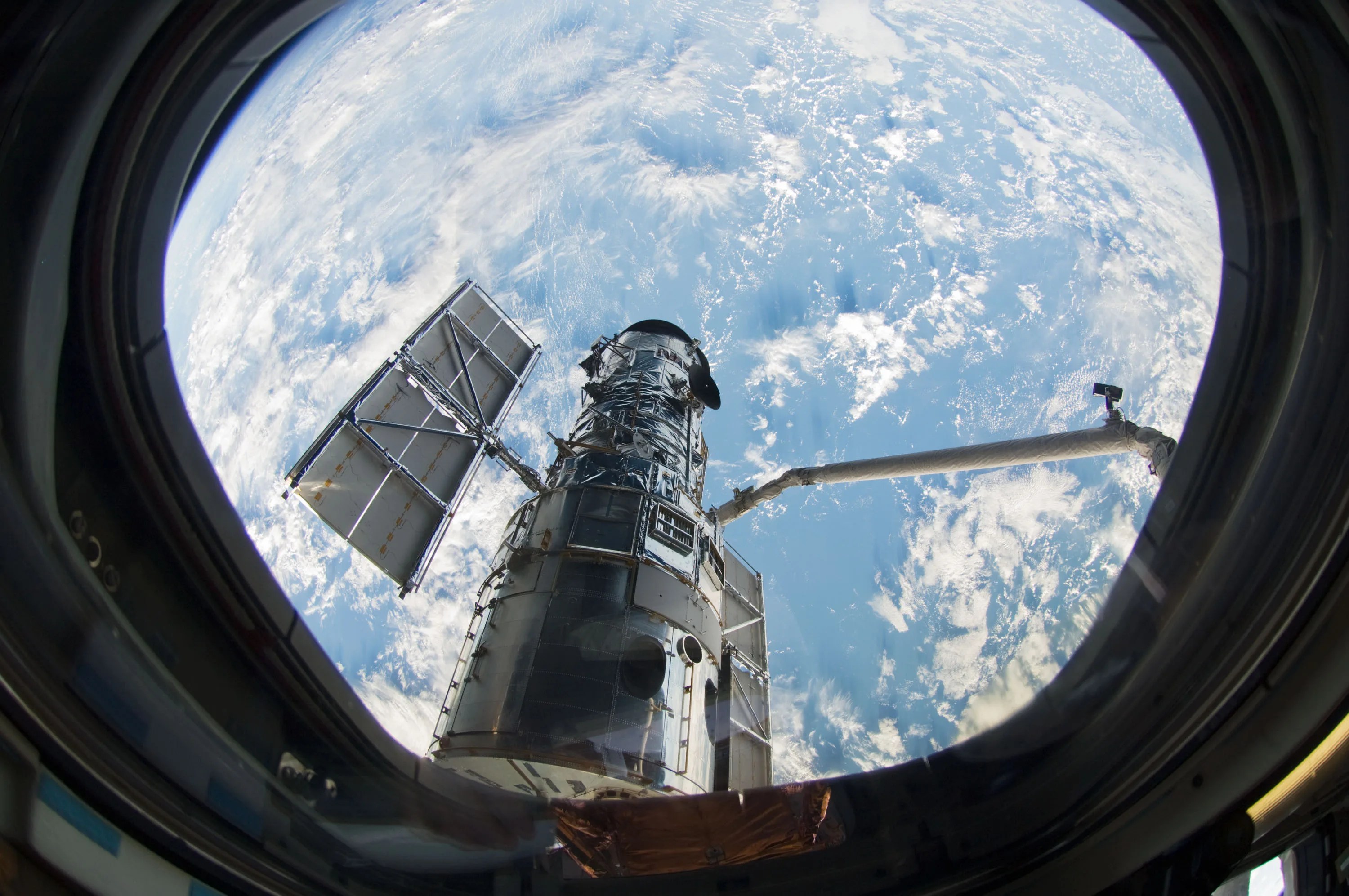
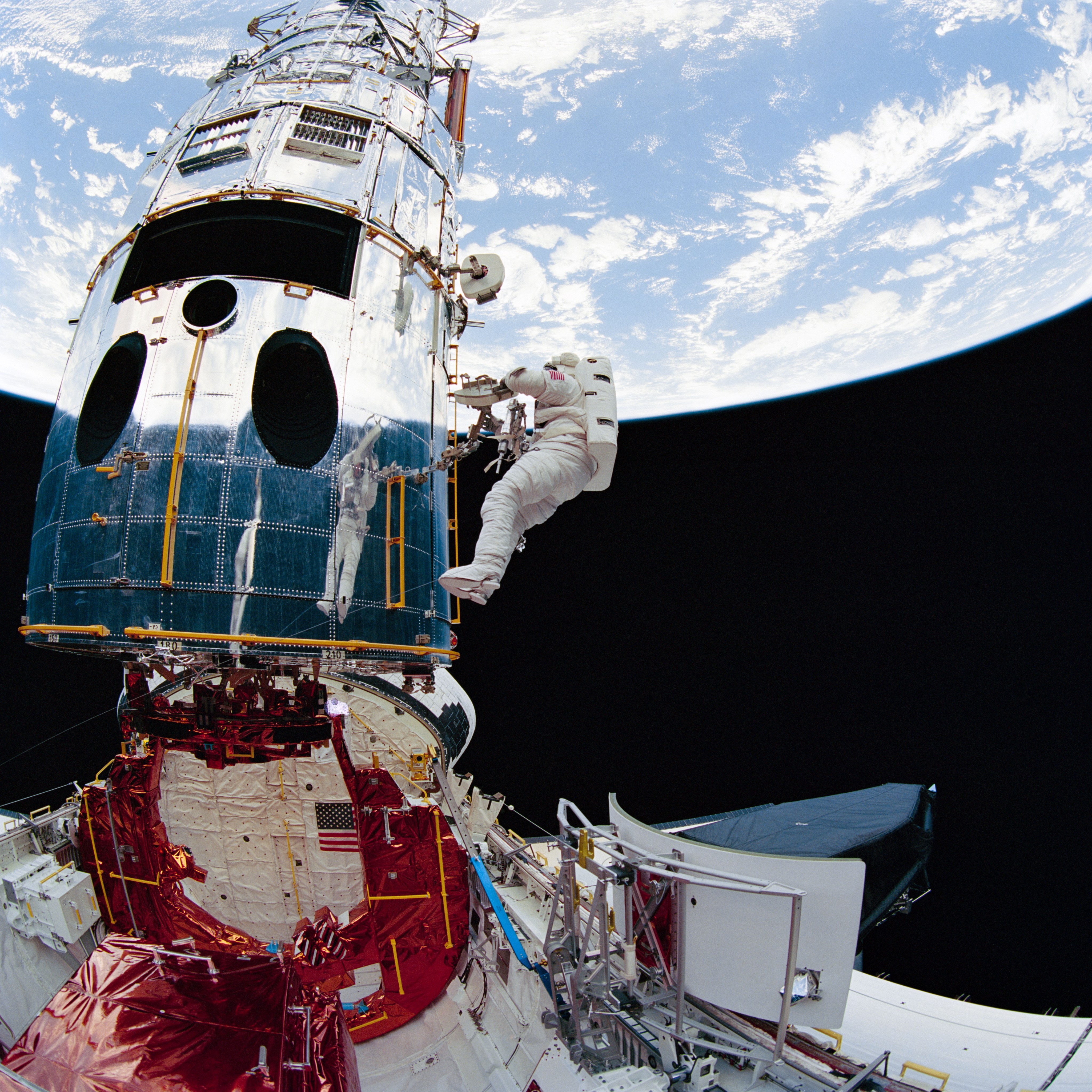
Robotic servicing missions are on the calendar for the future, but in some ways Hubble was a pioneer in robotic servicing as well. The Flight Support System developed for the shuttle’s cargo bay was a turntable device similar to a "Lazy Susan” that could rotate and tilt once Hubble was berthed to it to assist with servicing tasks. The shuttle’s robotic arm was equipped with a device called a Manipulator Foot Restraint, which let astronauts lock their boots into a secure platform with a lean, podium-like attachment for securing items like tools. Astronauts could then be moved via the robotic arm around and above the shuttle’s payload bay, where the telescope rested, and be oriented in the ideal way to access the telescope while keeping their hands free. While these activities on Hubble required a human at all times, the marriage of such robotics with human repair tasks was an early step toward potentially turning certain tasks over to robots.
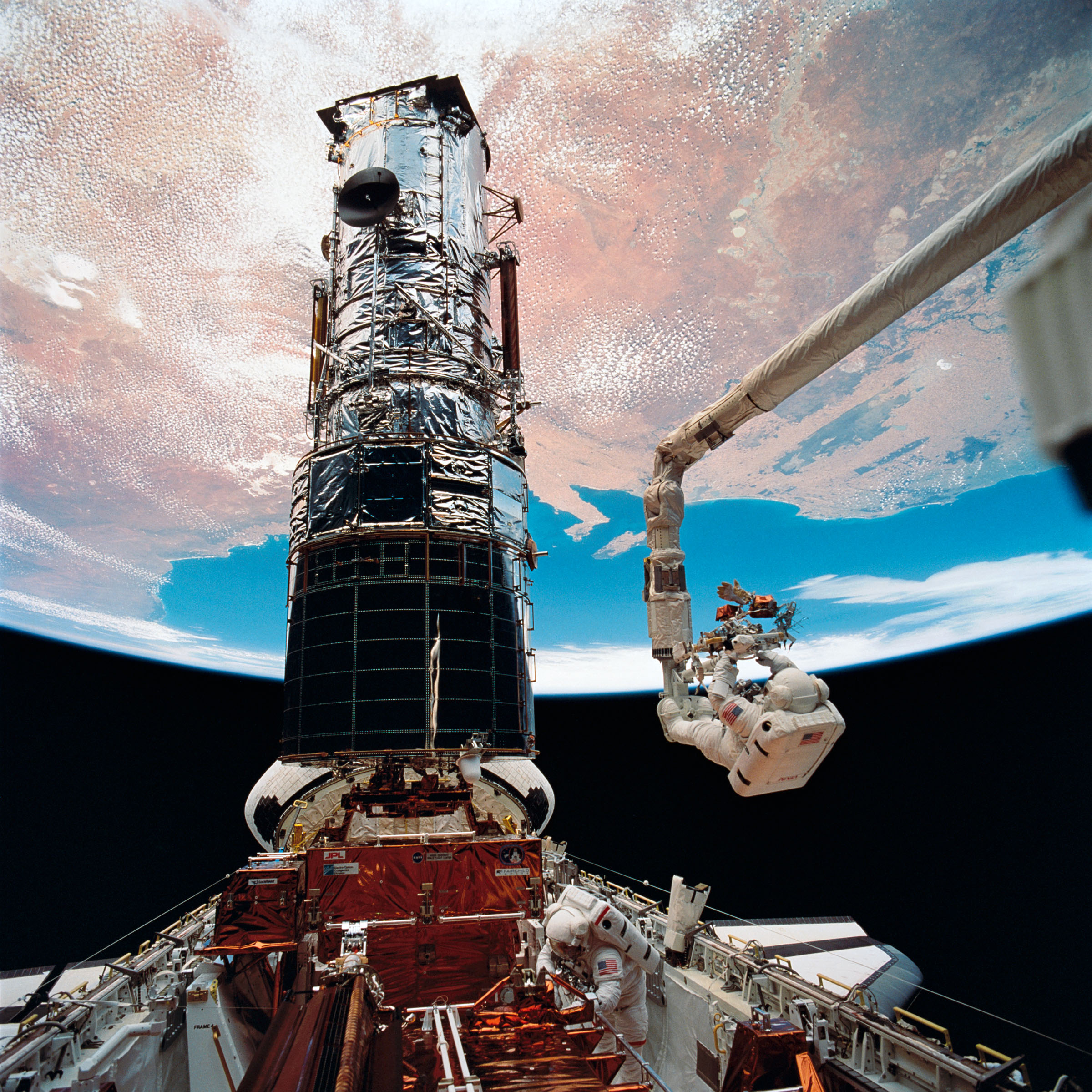
From launch through five servicing missions, the Hubble Space Telescope has always been a shining example of what humanity can accomplish in space. Thanks to Hubble, we have refined our techniques for operating in a weightless environment, learned how to accomplish once-unthinkable tasks, and found we can rise above adversity to reach even further than we imagined. As people set their sights on the Moon and Mars, Hubble has helped pave the way for the next chapter in human exploration of the cosmos.
Learn More About Hubble Servicing Missions
Want more Hubble?
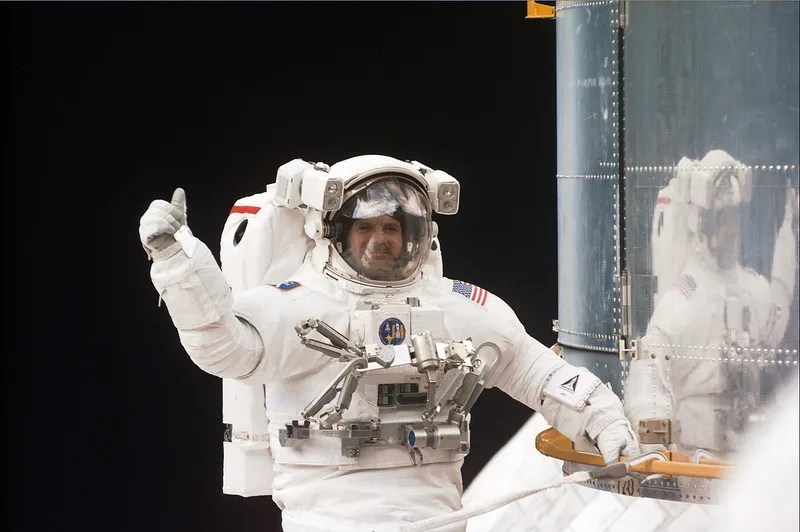
Hubble Astronaut Fun Facts
Play this astronaut trivia game and test your knowledge of Hubble astronauts?
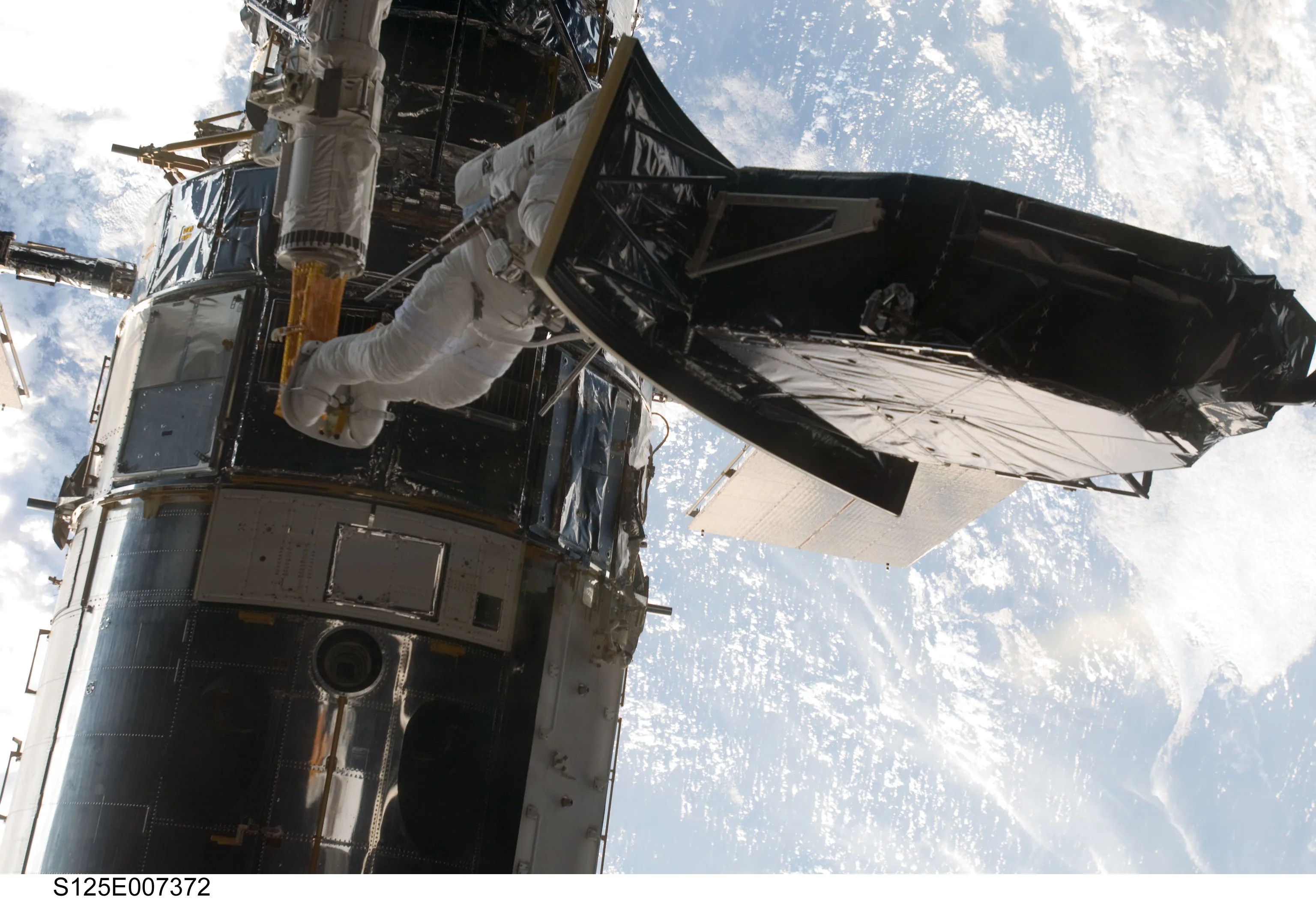
Hubble's Scientific Instruments
Hubble holds five different types of instruments including cameras, spectrographs, photometers, interferometers, and fine guidance sensors.

Control Center 360º Tour
Go behind the scenes at the heart of Hubble 0perations with this 360-degree virtual tour.
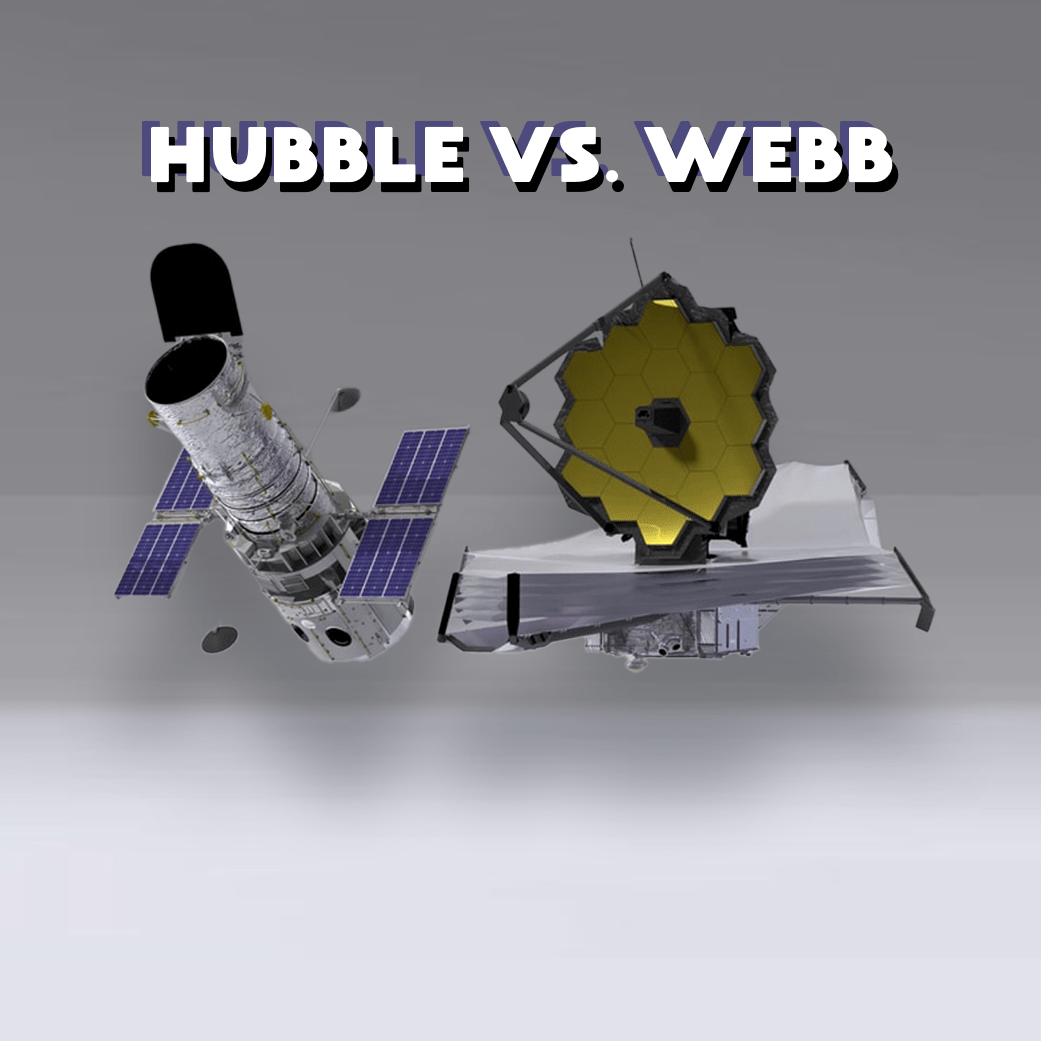
Hubble vs. Webb
Discover how Hubble and Webb complement each other and work together to explore the cosmos.